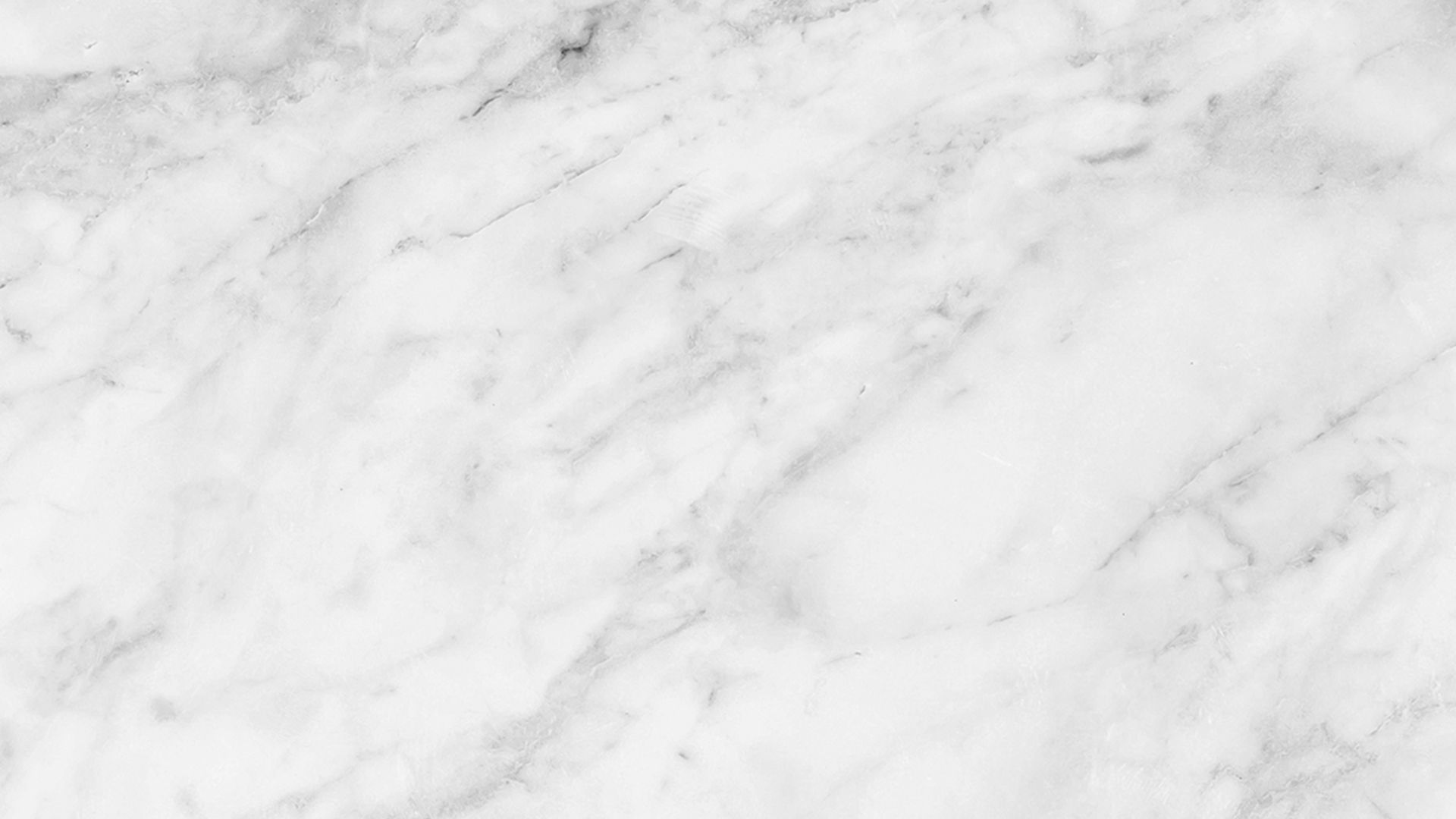
2024/25 GALLERY Judith Paisley
New Works ... Raku - Naked Raku - Saggar - Pit/Barrel Fired - High Fire Stoneware - Porcelain
Double click on pics to see full view and details
Saggar Firing
Now this is an exciting firing - an opportunity to experiment with a vast array of different organic materials to influence (not control) an incredible outcome.

Saggar Firing...
is a playground, an open invitation to experiment.
(having said that at this point – I must mention strict codes of safety and appropriate safety equipment are essential when dealing with toxic chemicals).
Pots designed for Saggar Firing are best burnished in order to highlight its finest beauty when polishing the final piece. The artwork is placed in a saggar pot with lid, made of preferrably grogged stoneware clay which can tolerate high temperature firing and rapid thermal changes.
The pieces are placed on a bed of sawdust preferably pine wood shavings, then a variety of materials – chemicals, salts, metals and organic materials placed around in close proximity of the surface of the pots. During the firing process, the combustibles, salts and chemicals react with each other producing serendipitous markings and a rainbow of colours on the artwork. The saggar traps the smoke and fumes, allowing penetration
of the clay body. I fire mine in the gas raku kiln
slowly up to 250c then increase every 10 mins till
870c then hold between that and 925c for 20 minutes then turn the kiln off and leave the saggar to cool off naturally. Let me say at this point to save any disasterous cracks in your saggar pot, cover all the port holes of the kiln completely. (I learned the hard way) When cool enough (around 100c I take it out and after much ooing and aahing and the occasional hmmm! I clean up and wax.
The results of each firing are different and there are no two pieces alike.
If your first firing is a success, it leaves you aching for the next opportunity.
As with most alternative firings, I have found whilst researching, there appears to be no set rules, different schools of thought and contrasting methods due to varying influencing factors. Experimentation in ceramics is always the key factor, in particular with Saggar Firing.
ORGANIC & other MATERIALS
That can influence different
colours and effects...
•Banana skins
•Seaweed
•Flower petals
•Steel wool
•Spanish Moss
•Horsehair
•Copper wire
•Twine
•Salts and oxides, copper, red iron oxide
•Sawdust - pine shavings
Ferric Chloride
Be creative – experiment.
I at this stage have not used ferric chloride as I would rather try and achieve colour from the fuming of the salts with the organic matter.
Naked Raku

Bearing one’s soul......
Naked Raku is a more complex method of Raku. The pots are fastidiously burnished at leather-hard stage until shiny. I have a favourite polishing stone I use for burnishing. Although not necessary, I prefer to use Terra Sigiallata and burnish which gives an incredible finish. (this however will alter your firing time) Which ever method you chose to burnish, the time spent on this process will be reflected in the final piece.
The pot is then bisque fired to about 800c to 895c depending on your glaze, a temp lower than for normal raku. Any higher and you will lose the burnishing. A slip is then applied to the pot and after 24 hours a layer of raku glaze is added on top of the slip. The slip acts like a separation layer between the clay and the glaze, preventing the glaze from melting and adhering to the surface of the clay. The pot is then placed in the raku kiln and fired to approximately 750-800C when the glaze starts to bubble. Don't go above 800c or the glaze may fall off during the firing. (trust me - I've been there) If using terrasigiallata, you need to start watching your work carefully after 700. At about 600 your kiln should be starting to glow red. At 700 glaze starts to change colour. Start watching carefully from 750 when the glaze starts to melt and around 800 it should be nice and shiny and ready to pull. I pull around 795 - 815 leave it any longer, with terra sig being a more slippery surface as soon as it hits the cold air it is likely to shed the glaze earlier.
(At this point I have to say the above temperatures may change with different ingredients in a glaze recipe -I have just experienced a frustrating run of misfires
due to a change in a frit and kaolin and am now firing to just over 800....so my
suggestion is TEST TEST TEST first to see what works for you and your recipe.)
It is then quickly but carefully removed from the kiln with tongs and gloves and placed in a reduction chamber/bin. In the reduction process, smoke penetrates the cracks of the glaze, through the slip layer into the clay leaving irregular crackle patterns on the surface.
After about 10 minutes, take the pot out
and pour water over the outside of the piece which will encourage the layer of slip and glaze to pop off, revealing patterns created on the bare / nude clay ......... hence the name ‘Naked Raku’. The surface is then cleaned and waxed.
(careful not to get water inside a vessel
as it can't escape - this may cause cracking, just pour over the outside.)
I know some people fire to a higher temperature, but glaze recipe plays a big part in this. Once again experiment with the temperature with whatever recipe you use and see what works for you.
Thickness of slip can also be a factor in
premature shedding of glaze during firing.
SEE next page for notes on Terra Sigiallata
Raku Firing

The Raku firing process... requires a kiln fueled by propane gas or wood fired with the pottery remaining in the kiln for around 60 minutes up to aprox (1000C). This varies depending on required glaze finish. It is then carefully removed with protective gloves and raku tongs and ushered very carefully to metal reduction chambers / bins full of combustible materials. The heat from the pots ignites the material and bursts into flames then the bin is quickly sealed. As the fire consumes the oxygen within the can it also draws the oxygen out of the clay. After a few minutes, lift the lid of the bin and reoxidize, but be very careful as it will flair up and catch fire again, then quickly close the lid. This process will be the final post fire reduction, which creates the unique carbonized crackling and look of Raku. The piece is carefully removed after about 20 minutes, then cleaned with cold water, which freezes the patterns created during the reduction stage.
Reduction Methods - these vary with
different glazes and sometimes a matter of preference.
I like to use newspaper with a base of
sawdust to initiate the flame.
I find newspaper gives a cleaner crackle,
as scarring can some-times occur with sawdust if immersed too soon whilst the glaze is still molten.
Black Copper Matte
Again different people have their preferences with regards reduction of this glaze. I like to use the newspaper again and make sure the flames have plenty of time to lick the sides of the piece to induce lots of colour before the final reduction cover goes on. If you use sawdust, you need to move it about, covering and uncovering with sawdust to introduce plenty of oxygen before covering for final reduction. When cooled, this should just be brushed to remove any sawdust, not immersed in or cleaned with water. (different recipes of copper matte sometimes actually work better with sawdust - again experiment.)
SPECIAL NOTE:
Copper Matte fininshed pieces should not be exposed to sunlight as it will continue oxidizing and eventually fade. If kept inside, out of the direct light it should last for many years.
I still have one of my first copper matte pieces I raku'd over 8 years ago and it is just as brilliant in colour as it was then. It has been kept inside out of the sunlight.
WARNING.........
With all of the above firings, extreme care must be taken and mask, gloves, and goggles should be worn, in particular when removing work from kilns and during the reduction period.
Do not become complacent, these are Toxic Chemicals, Carbon and YOUR Health you are dealing with.